We are a world leader in high precision optical manufacturing, delivering custom optics to a wide range of innovators around the globe. Meeting these goals demands the right people. Teamwork, adaptability, and an enthusiastic approach to problem-solving are central to the Optimax culture. But what unites all our employees best is a hunger to continuously learn. We strive to find driven individuals who are committed to lifelong learning; who will continue to add value in their work throughout long and successful careers.
REQUEST A QUOTE
Our quotes are structured to offer standard pricing and delivery – quicker delivery options are available upon request.
LEARN FROM THE EXPERTS
Discover how Optimax is changing the future of optics, and view our extensive library of resources.
JOIN OUR TEAM
We are looking for individuals that are committed to lifelong learning and creating value through their hard work.
An Introduction to Optical Prisms
Optical prisms differ from traditional lenses in that they have neither a spherical surface nor an axis of symmetry. Instead, they comprise two or more nominally plano surfaces divided by a wedge angle. This alters the language used to define and specify optical prisms, and it typically increases production time due to increased part complexity and a greater number of sides requiring precision finishing.
The significance of these geometries is that they will reflect or refract light, resulting in several distinct functions: dispersion, deflection, reflection, and rotation. These go on to serve critical applications in dual channel instruments, anamorphic systems, imaging systems, and any other application where beam steering and/or image manipulation is needed.
Specifying Optical Prisms
Optical prisms vary dramatically by size, shape, and number of surfaces. Defining the part geometry requires a careful selection of directly measurable physical parameters, including linear dimensions of the plano surfaces to theoretical sharps (the intersection that would exist between the two if the corner was not beveled). Manufacturers must also specify part thickness, which is the depth of separation between the two plano surfaces at a single point on the optic. At Optimax, we choose to specify the thickest edge as it offers ease-of-measurement access, but we can specify our optical prisms by the centerline thickness, or the thinnest edge if necessary.
The geometry of two-sided wedges can be defined by an angle and a thickness.
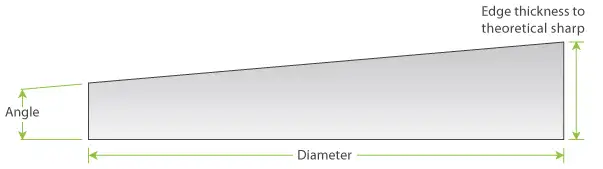
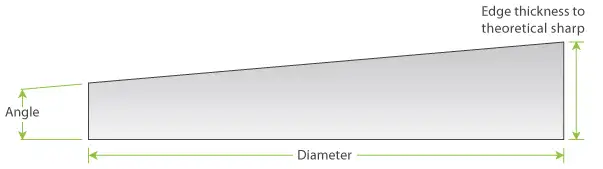
Image above: Minimum Specifications for Wedges
Manufacturing Aspheric Lenses
At Optimax, we specialize in manufacturing optical prisms up to 300 mm in diameter, and with our state-of-the-art grinding and smoothing technologies, can deliver prisms in a variety of complex geometries to tightly-defined surface flatness.
We routinely fabricate such prisms as:
Common functions include:
FIND THE OPTIC SPECIFICATIONS RIGHT FOR YOUR NEEDS:
Prisms Manufacturing Limits Prisms Tolerancing Limits Manufacturing Tolerance ChartTechnical Expertise
Do you want to learn more about our optical manufacturing innovation? Refer to our Knowledge Center to read technical papers on, aspheres, business leadership, coatings, freeform optics, innovative optics manufacturing, and lens tolerancing & inspection.
Manufacturing the Future
At Optimax, we are manufacturing the future, creating the highest precision optics underlying high-tech systems in key markets and applications. We offer rapid and expedited delivery upon request and are committed to our customers in the long term.
Submit an RFQ to start building your relationship with one of the world’s foremost manufacturers of custom optics.