We are a world leader in high precision optical manufacturing, delivering custom optics to a wide range of innovators around the globe. Meeting these goals demands the right people. Teamwork, adaptability, and an enthusiastic approach to problem-solving are central to the Optimax culture. But what unites all our employees best is a hunger to continuously learn. We strive to find driven individuals who are committed to lifelong learning; who will continue to add value in their work throughout long and successful careers.
REQUEST A QUOTE
Our quotes are structured to offer standard pricing and delivery – quicker delivery options are available upon request.
LEARN FROM THE EXPERTS
Discover how Optimax is changing the future of optics, and view our extensive library of resources.
JOIN OUR TEAM
We are looking for individuals that are committed to lifelong learning and creating value through their hard work.
What are our Coating Capabilities?
We produce custom anti-reflection coatings; beamsplitters; metal mirrors; laser line and broadband dielectric mirrors; and filters. We produce functional coatings for the full spectrum, from DUV to mid-IR applications. Our coatings have been used successfully in some of the most demanding space, defense, high-power laser (HPL), medical, and semiconductor applications. Learn more about the industries we serve.
Our Coating Technologies
Optical Coating Capabilities
Engineered Solutions
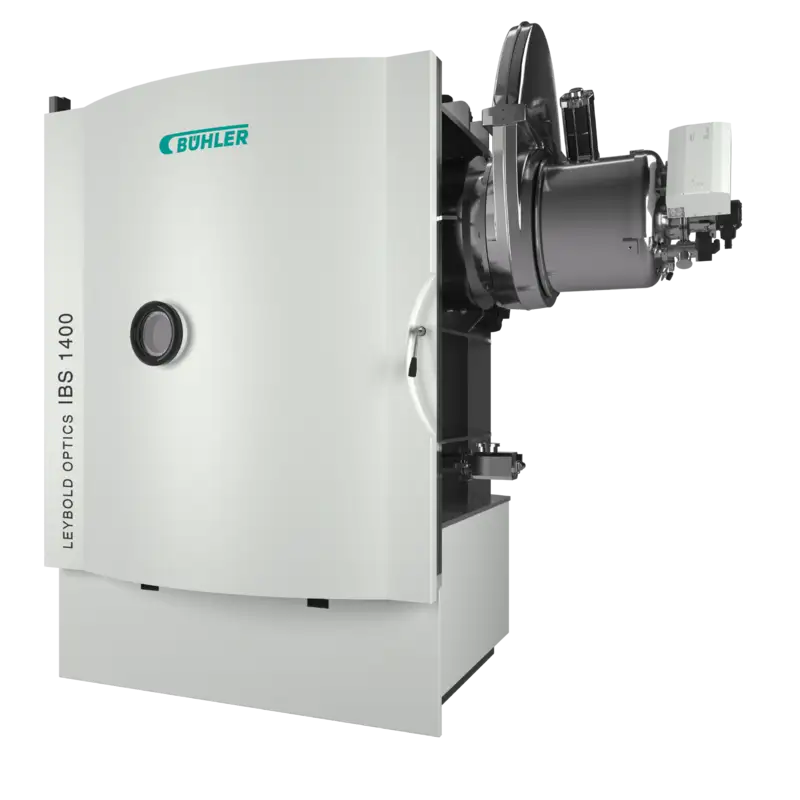
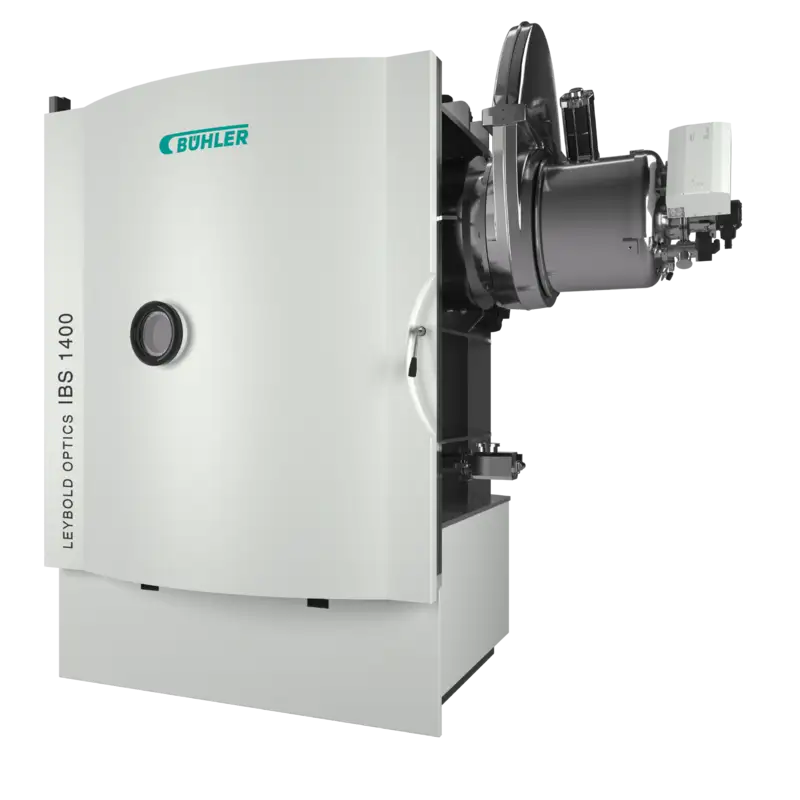
Featured Engineered Solution
Ion Beam Sputtering (IBS) Coatings
Optimax low-stress Ion Beam Sputtered (IBS) coatings enable tight post-coating wavefront control on complex mirror geometries while maintaining low absorption and high CW laser damage threshold.
Applications of Optical Coatings
Optical engineers must go through a detailed decision-making process when designing high-precision optical components. At Optimax, we have years of experience supporting manufacturing teams in critical application areas with high-performance optical coatings that stand up to the harshest operating conditions. We consider the needs of our valued customers at every step of the fabrication process and strive to deliver optical coatings which go beyond standard specifications.
CW High Power Laser Coatings
Our continuous and pulsed wavelength (CW/PW) high-power laser coatings have been applied in some of the world’s most demanding CW laser systems, offering a laser damage threshold of >10 MW/cm2 plus low defect counts and low absorption.
wdt_ID | CW High Power 1070 nm Antireflection (AR) & Dielectic Mirror (HR) Performance | - |
---|---|---|
1 | Laser Damage Threshold* | >10MW/cm² |
2 | AR Coating Absorption** | < 2 ppm |
3 | HR Coating Absorption** | < 5 ppm |
*As tested at Penn State EOC, 17kW laser, 0.5mm spot size, 63.5 mm2 raster area.
**Max peak absorption as measured using Photothermal Common-Path Interferometry at Optimax, 2 mm scan length. Measurements verified by Stanford Photothermal Solutions.
Pulsed High Energy Laser Coatings
Thousands of Optimax coated optics are used in the highest energy pulsed lasers in the world. Our coating and cleaning processes have been developed under National Ignition Facility and Omega Laser guidelines to achieve low defect counts, low absorption, and high laser damage thresholds.
wdt_ID | Type | Wavelength | Pulse Lengths | Typical Specifications | Optimax Best Performance |
---|---|---|---|---|---|
1 | HR | 1064 nm | 10 ns | >40 J/cm² | >125 J/cm² |
2 | AR | 1064 nm | 10 ns | >25 J/cm² | >65 J/cm² |
*Pulsed testing results are fluence at which 0 defects were observed at 150x magnification after raster scanning with a 1mm beam across 2500 sites at 5-10Hz per LLNL Spec NIF-5008633 MEL01-013-OD protocol
UV/DUV Lithography Coatings
We have also developed highly uniform filters for ultraviolet and deep ultraviolet (UV/DUV) lithography applications, supplying the world's lithographic engineers with optical substrates qualified for more than a billion cycles of KrF illumination with no spectral degradation.
Space Qualified Coatings
Space can be a harsh environment for optical coatings. Our engineering team has successfully provided antireflection (AR) coatings for a wide range of space applications. Our coatings have been qualified for many missions, demonstrating:
Technical Expertise
Do you want to learn more about our optical manufacturing innovation? Refer to our Knowledge Center to read technical papers on, aspheres, business leadership, coatings, freeform optics, innovative optics manufacturing, and lens tolerancing & inspection.
Manufacturing the Future
At Optimax, we are manufacturing the future, creating the highest precision optics underlying high-tech systems in key markets and applications. We offer rapid and expedited delivery upon request and are committed to our customers in the long term.
Submit an RFQ to start building your relationship with one of the world’s foremost manufacturers of custom optics.